Inspection Services
We have expertise for sourcing, sampling, quality checks, Inspections and shipment co-ordination. Dzire Trends is a one stop shop for all importers, we act as their Indian counterparts and deliver a wide range of inspection services. We have a strong vendor base across India for sourcing of Knitted Products in different type of Fabric, Woven Products like Shirts, Kids Products, Nursery Products , Denim & Jackets. With our strong business associations with the countrys best suppliers, exporters and manufacturers dealing in a vast variety of products we bring the choicest range of products to our buyers offering them the best of designs, quality and prices.
Why quality inspection is important?
Quality Inspection in India is important simply because poor quality increase global cost of your order and mainly you didn’t expect it in advance. In the same time defective products give you trouble with your final customers and you lose their trust by providing them non-confirm products. By inspecting products before shipment (Initial Production Inspection, During Production Inspection, Pre Shipment Inspection, Container Loading Inspection, 100% Full Inspection, Quality Assurance) you reduce considerably risks related to quality product in India
The costs associated with import risks and product recalls are definitely reduced thanks to our solutions for an affordable price. Indeed, on a production of 20,000 USD amount, spend only 358 USD to decrease significantly risks is definitely the best solution to secure our order without burning your cash in constant journey from your place to your factory location.
India Quality Control’s inspection report allows you to get a status of your production and an accurate situation of your products before you have to pay the balance of your goods. It’s not only when your goods arrive to their destination port that you will have to send back your container, waste your time, run behind your supplier.
The principle involved in quality inspection is the early detection of defects and support of on-time delivery.
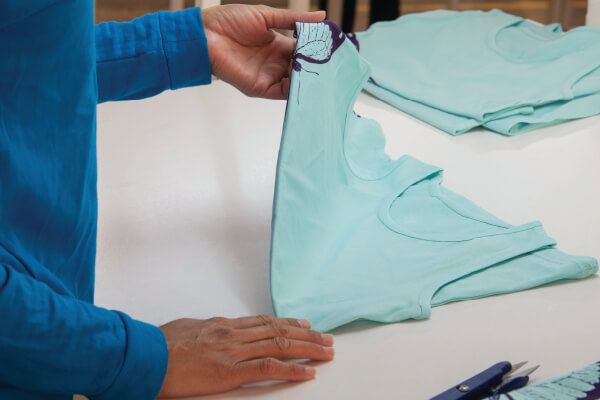
Initial Production Inspection
What is an Initial Production Inspection?
An Initial Production Inspection (IPI) is conducted at the very beginning of production, ideally after the vendor verification process (factory and/or social audit) has been completed.
The objective of an Initial Production Inspection or Pre Production Inspection (PPI), is to identify defective materials or components prior to the production process, thereby minimizing the risk of non-conformities and allowing for timely corrections where necessary. It can also identify if your vendor has correctly understood your order, avoiding miscommunication and ensuring that any deviations from the customer? specifications are addressed early.
During Production Inspection
During Production Inspection (DPI)
During Production Check or DPI improves production processes and quality.
This service is best for large quantity shipments, product lines with continuous production, strict requirements for on-time shipments, and as a follow-up if poor results are found during Pre-Production Inspection. Dzire Trends will inspect the production batch and examine products in the line for possible defects, normally when 20% of the merchandise is completed. We will identify if there are any deviations, and offer advice on corrective measures and recheck any defects during Pre-Production Inspection to confirm they have been rectified.
At all stages of the production cycle our Dzire Trends inspector will produce a complete and detailed inspection report, together with a photographic record within 24 hours of the inspection allowing you to see the work undertaken. We have a network of inspectors and can arrange your inspection within three working days of receiving your request. A Dzire Trends DPI inspection will provide you with an expert view prior to production giving you a quality safety net and the confidence that your suppliers will provide you with top quality products supporting the values of your brand.
Pre Shipment Inspection
Pre Shipment Inspection (PSI)
Pre-shipment inspection, (also spelled pre shipment inspection) or PSI, is a part of supply chain management and an important quality control method for checking the quality of goods clients buy from suppliers.
PSI ensures that production complies with specifications of the buyer and/or the terms of a purchase order or letter of credit. A final random inspection (FRI), checks finished products when at least 80% of an order has been produced and export-packed. Samples are selected at random, according to standards and procedures. Pre shipment inspection can diminish risks inherent to Internet commerce like phishing and fraud.
Dzire Trends provides pre-shipment inspection services to governments as a way of protecting import revenues for themselves and their citizens.
Container Loading Inspection
What is a Container Loading Inspection (CLI)?
During a Container Loading Check, Inspector will select boxes at random to confirm each carton bears the quantity of product ordered, the quality matches the specifications and/or approved sample provided by you, and that all material contains the correct barcodes, labelling, and packing materials. The entire container loading process is strictly administered; ensuring all products paid for makes it on the truck. A CLI reduces risk of damage during shipment.
Cargo Container Loading Supervision and Check
Dzire Trends cargo container loading inspection has been established for those clients that not only require reassurance during the container loading process, but also need confirmation that safety and quality requirements are met and that correct goods handling procedures are put in place and adhered to.
All of Dzire Trends inspectors are fully trained not only to supervise but to closely monitor the loading process. Before shipping they check the:
- Quality and condition of packaging
- Quality and condition of your goods.
- Adherence to correct goods handling procedures
- Condition of the container your goods are being transported in, including safety and cleanliness
- Correct loading of your goods and also verify all documentation
100% Inspection
100 percent inspection full check service is commonly used to avoid shipping non-conforming product. Each of the items produced is measured and judged to be either conforming or non-conforming. The conforming items get shipped, and the nonconforming items get set aside for use as factory-authorized replacement parts or some other equally ignominious fate.
The quality of goods are checked unit by unit, which covers product description, style & color, workmanship, quality, function, label, package, size measurement etc, to make sure 100% of the goods meet your specified quality requirement.
100% inspection (full inspection) is needed when:
Quality Assurance
As the sourcing, buying and Indian inspection agents / agency (3rd party inspection agency) for products such as home furnishings, home textiles, furniture, home decor, glassware, gift items and a whole range of accessories, we take the full responsibility from selecting a vendor, selecting the good quality raw material, and sending the initial production pieces it to the client for approval and on their approval starting mass production.
Quality is our priority. We work as per the requirements and specification from our valuable clients. Our group of experienced professionals conducts rigorous quality checks at every stage of production and also after the final product is made the entire consignment is checked and timely dispatched. The process of Quality assurance follows as: